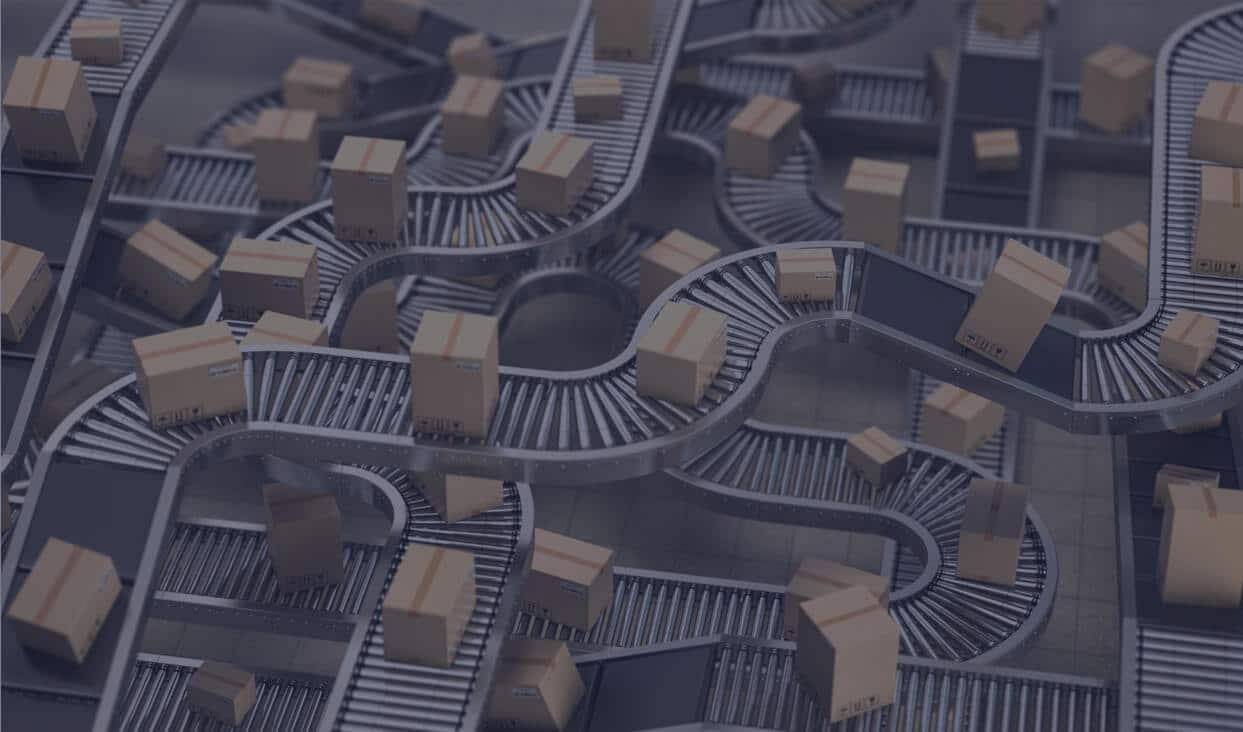
Material flow analysis – advice from experts
We offer advice on material flow analysis
Material flow analysis as an important tool
Companies cannot avoid a material flow analysis if they want to work economically. It should therefore be seen as the basis for process optimization. If material is not used and therefore not in flow, no money can be earned with it. Material has to move, and it has to move quickly and directly. A material flow analysis is an important tool for ensuring this and taking the right steps. This enables material flow costs to be determined and, if necessary, redirected to other areas. The positive result of this analysis can therefore only be the saving of costs, time and resources. Incidentally, this should be carried out at regular intervals.
The advantages of the analysis
Production processes never stay the same, they are constantly changing. This change in conditions means that the various areas such as production, intralogistics and storage must be adapted accordingly and weak points identified. The advantages of material flow planning are obvious:
- Avoidance of delays
- No unnecessary waiting times
- Standstill is avoided
- Reduce production, transportation and storage costs in advance
- Avoidance or reduction of price increases
The steps of a material flow analysis are usually the same. First, the objectives are formulated, then the expected results are determined. A database is then created. By examining the system processes, an inventory is carried out and evaluated. After documentation and graphical representation, the results are presented. In this way, the deficits become visible and optimization can begin.
The digital twin as a tool for material flow analysis
We also offer the option of optimizing your material flow using a digital twin. This can be realized entirely according to your wishes and supports the classic material flow analysis as a tool. This offers you various advantages, such as
- Higher data consistency & quality
- Improved efficiency in assessment & vulnerability analysis
- Less time required to evaluate the data
- More efficient consideration of changes
We have specialized in the Plant Simulation software from Siemens and visTABLE from Plavis GmbH. This enables us to take all details and data for the material flow analysis into account and to work according to the current state of the art at all times.
Are you interested?
Get in touch with us!
Alexander Follath
Senior Consultant
We create a material flow analysis for you
We at Bross plan your material flow according to the established VDI 3633 standard. From consulting to implementation, we are your reliable and competent experts for material flow analysis, material flow simulation and material flow optimization. Your reliable and competent experts. Our many years of experience speak for themselves. You too can optimize your workflows so that you can look forward to a healthy company in the long term. Turbulent changes in the market must be countered by appropriate action. We want to be your reliable partner for this.
FAQ
What does material flow mean?
VDI Guideline 2689 defines material flow as “the interlinking of all processes involved in the extraction, processing and distribution of goods within defined areas.” Material flow refers to the process in which materials and goods are transported from their starting point to their destination. This flow can take place within a company, e.g. from the warehouse to the production facility. It can also take place between different companies, e.g. from the supplier to the customer. An efficient flow of materials is the backbone of any productive business activity. A smooth flow of materials is important for the success of a company. This applies to production, logistics and sales. Efficiency plays a decisive role in profitability. But what exactly is material flow and what elements are involved?
The material flow includes both physical movements (transportation, storage, handling) and the associated information flows.
The physical flow of materials refers to the actual movement of materials and products. This includes the transportation of materials from one location to another. The materials are stored at various points along the flow. In addition, the materials are handled during transportation and storage.
Together with the physical flow, there is also an information flow. This includes all the information required to control and coordinate the material flow, such as stock information, delivery times and production plans.
What is part of the material flow?
The material flow includes various elements that work together to ensure a smooth and efficient process. These include:
Transportation is a central element of material flow. It includes all activities associated with the movement of materials from one place to another. This means that materials are brought from a supplier to the factory. Materials are also moved within a warehouse or factory. Finally, finished products are transported to the customer.
Storage is another important part of the material flow. It refers to the storage of materials and products along the material flow. These activities are associated with it. This can include the storage of raw materials, intermediate products and finished products.
Handling refers to the physical manipulation of materials during transportation and storage. This includes the loading and unloading of vehicles. It also includes transferring materials from one means of transportation to another. And stacking and sorting materials in the warehouse.
Planning and control is crucial for the efficiency of the entire process. It is about planning the best route for the transportation of material. To do this, the required resources must be determined. In addition, the various activities associated with material transportation must be coordinated.
Why is material flow analysis important?
A well-organized material flow is crucial for operational efficiency. A good material flow shortens production times, reduces warehousing costs and increases productivity. The basis for identifying optimization potential is material flow analysis. This can be supported systemically by material flow simulation, for example. This is done by ensuring that materials flow efficiently and smoothly through the production process. As a result, bottlenecks can be avoided and production processes optimized. A good flow is therefore crucial for the success of a company. An efficient material flow can increase customer satisfaction. This means that the right products are available in the right place at the right time.
Improvement in production times
Material flow optimization can significantly reduce the time it takes to manufacture a product. This can help to increase production capacity and shorten throughput times.
Reduction in warehousing costs
Efficient flow can help reduce the amount of materials and products that need to be stored. This can help reduce warehousing costs and free up capital that can be used for other purposes.
Increase in productivity
A well-organized material flow increases productivity. It ensures that the right materials are available in the right place at the right time. This can help to avoid delays and downtime and increase overall productivity.
Improving customer satisfaction
A good material flow ensures that products reach the customer on time and undamaged. This in turn increases customer satisfaction. This can help to strengthen customer loyalty and promote business growth.