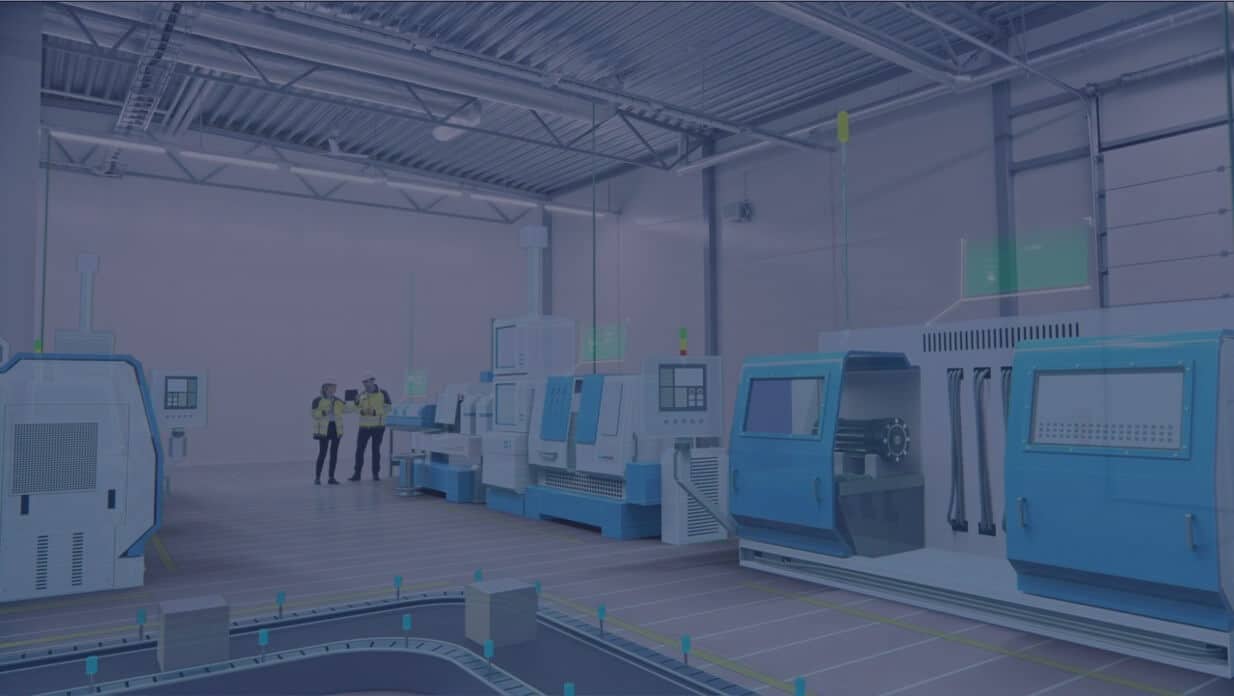
Bross are your logistics & factory planners
State-of-the-art planning by Bross Consulting
Well-known companies rely on Bross
We are Bross Consulting
Bross Consulting is a technical management consultancy for the planning, optimization, digitalization and implementation of production and logistics systems. Our team of experienced logistics and factory planners offers customized solutions tailored specifically to your challenges. We combine technical know-how with strategic vision to improve your operations and increase your competitiveness.
Our services at a glance
Bross stands for excellent services in the three areas of production, logistics and digitization. Our logistics and factory planners work closely with our clients to analyze their processes, develop concepts and implement optimizations. We always use state-of-the-art technology and innovative tools for factory planning and material flow analysis.
Our methods are effective across the industry
Our goal is to help our clients overcome the challenges of the markets – such as a high diversity of variants and high cost pressure. We achieve this by identifying practical and customized solutions that are tailored to the specific needs and objectives of our clients. At Bross Consulting, we pride ourselves on providing not only technical but also strategic solutions to our clients in all production and trading industries. We look forward to helping you with your production and logistics challenges.
Bross’ results are scientifically sound and practically implemented
Thanks to our scientific proximity to the Technical University of Munich and Munich University of Applied Science, we always have our finger on the pulse of the times and offer you state-of-the-art solutions. As a client, you are interested in functioning solutions that differentiate you from your competitors. We show you these solutions and create confidence in new technology, such as the automation of your warehouse logistics. When designing and introducing new technology into your company, a systematic approach is a basic requirement. The methods used by Bross are based on industry standards and have been tried and tested in numerous industrial projects.