KVP – Kontinuierlicher Verbesserungsprozess
KVP, Kontinuierlicher Verbesserungsprozess oder auch Kaizen (vom japanischen: KAI = Veränderung; ZEN = das Gute), bezeichnet sinngemäß den Ersatz des Guten durch das Bessere. Basis hierfür sind gelebte, ständige, kontinuierliche Verbesserungmaßnahmen, die in kleinen Schritten Prozess-, Produkt- und Servicequalität steigern, wie z.B. auch von der ISO9001 im Qualitätsmanagement gefordert wird. In Kaizen werden alle Mitarbeiter eingebunden (insbesondre ausführende Ebenen) und durch Schulungen dazu befähigt Probleme zu erkennen und eigene Detaillösungen (kleine Schritte) zu entwickeln, die dann zeitnah umgesetzt werden. Dies führt zu einem Kulturwandel im Unternehmen. Kaizen baut auf standardisierten Abläufen, Ordnung und Sauberkeit, einem visuellen Management und einem vorhandenen betrieblichen Vorschlagswesen auf und entwickelt aus diesen Elementen durch deren konsequente und dauerhafte Anwendung ein eigenes betriebliches „Lebensgefühl“ oder „Betriebsklima“.
Was sind die Voraussetzungen für KVP?
- Das gesamte Management muss sich zum KVP bekennen und die Mitarbeiter bei der Durchführung uneingeschränkt unterstützen
- Durch kurze und nachvollziehbare Entscheidungswege muss die Möglichkeit geschaffen werden KVP-Vorschläge zeitnah umzusetzen (Erfolgserlebnis für den Mitarbeiter)
- KVP benötigt Ideen und Wissen der Mitarbeiter, die nur kooperieren, wenn sie eine Arbeitsplatzsicherheitsgarantie haben
- Einfache Kennzahlen (Nachvollziehbar für die MA) sollten für die Formulierung von Zielen und die Bewertung der Ergebnisse genutzt werden
- Bei den Beteiligten muss das Bewusstsein bestehen, dass die derzeitige Situation Schwächen (Qualität, Service, Kosten) aufweist
Wie ist die Vorgehensweise zur Einführung von KVP?
1. Schritt: Vorbereitende Maßnahmen
- Umsetzung der 5S
- Erstellen standardisierter Arbeitsanweisungen für alle Vorgänge
- Visuelle Darstellung der aktuellen Situation durch Anzeigetafeln in der Produktion
- Einführung eines betrieblichen Vorschlagswesens mit Anreizen für die besten Ideen, um die Mitarbeiter in der Breite ohne Druck auf das Thema Verbesserungen anzusprechen und zu sensibilisieren
2. Schritt: Pilotphase
- Beginn mit kleineren, freiwilligen „Expertenteams“, die ausführlich geschult werden (soziale Kompetenz, PDCA, 7A…) und einige KVP- Pilotprojekte erarbeiten und umsetzen, die im Betrieb präsentiert werden
3. Schritt: Ausweitung auf das Unternehmen
- Schulungen weiterer Mitarbeiter (abteilungsweise) in Methoden- und Sozialkompetenz
- Teammitglieder des ersten Expertenteams leiten jeweils eine kleinere KVP-Gruppe
- Wöchentliche KVP-Gruppen-Meetings, bei denen gemeinsam Vorschläge in der Produktion diskutiert und ausprobiert werden
- Fortschrittstafeln zeigen die aktuellen Gruppenprojekte und -ergebnisse und dienen zum einen als direktes Feedback der guten Arbeit (Motivation), zum andern regen sie einen Wettbewerb zwischen Gruppen an
- Regelmäßige Schulungen und Veranstaltungen (Firma mietet jeden Dienstag eine Kegelbahn, Produktivitätsfest wenn ein gewisser Wert erreicht ist) um Wissen und Motivation der Mitarbeiter dauerhaft zu erhalten
Welche Probleme gibt es in der Praxis mit KVP?
KVP wird in vielen Unternehmen eingeführt und kurzfristig etabliert. Nach kurzer Zeit entstehen jedoch steigende Mobilisierungs- und Motivationsprobleme, die zu einem einstellen führen. Ursächlich hierfür sind vor allem das nachlassende Engagement sowohl im Management als auch bei den Mitarbeitern. Ursachen dafür sind:
- Mangelnde Rückendeckung/Unterstützung von Seiten des Top-Managements
- Fehlender Erfahrungsaustausch zwischen KVP-Gruppen
- Kein strukturierter und sichtbarer KVP-Ansatz im Unternehmen (keine visuelle Darstellung)
- Fehlende Zielvereinbarungen
- Organisatorische Änderungen, denen die KVP-Gruppen nicht folgen
- Keine Fortführung der regelmäßigen Methodenschulungen
- Keine zeitweise Freistellung für KVP-Maßnahmen (extra Zeit für KVP)
- Fehlende Anerkennung für Leistungen
- Hierarchische Organisationsstrukturen verhindern, dass „normale Mitarbeiter“ ihre Ideen einbringen
Um dauerhaft KVP zu erhalten, empfiehlt sich die Umsetzung von Kamishibai. Kamishibai enthält auf einer Karte alle Elemente eines Orts im Werk (Insel, Linie, Lager), d.h. eine kurze Nennung aller wesentlichen Prozessschritte dort. Die Kamishibai-Karte wird direkt vor Ort aufgehängt. Der Manager muss nun alle 2/4/8/12 Wochen (je nach Ausgestaltung) die Prozesse auditieren die auf der Karte stehen und sich selbst mit dem Ort beschäftigen und kann so Verbesserungen anstoßen. Die Ergebnisse werden in einem Management-Raum für Kamishibai präsentiert. Das nicht ausfüllen und entnehmen einer Karte fällt so in der Produktion und im Management auf. Neue Karten werden anschließend verteilt.
KVP mit PDCA
Ein wahrgenommenes Problem kann mittels des PDCA-Zyklus (Deming-Rad) systematisch angegangen und gelöst werden, Verschwendungen werden eliminiert. Das Vorgehen erfolgt in vier Schritten:
- Plan: Quantitative Beschreibung der Ausgangssituation Zunächst wird die Situation – möglichst in Daten – beschrieben und die darin offensichtlichen Probleme abgeleitet. Auf Basis der Daten werden der Zielzustand und Maßnahmenpakete erarbeitet und vereinbart, d.h. wer, was bis wann zu tun hat.
- Do: Die Lösung wird probeweise umgesetzt
- Check: Nach Umsetzung wird durch Soll-Ist Vergleich geprüft ob das neue Vorgehen besser ist, als das bisherige
- Act: Die neue Vorgehensweise wird allgemeinverbindlich
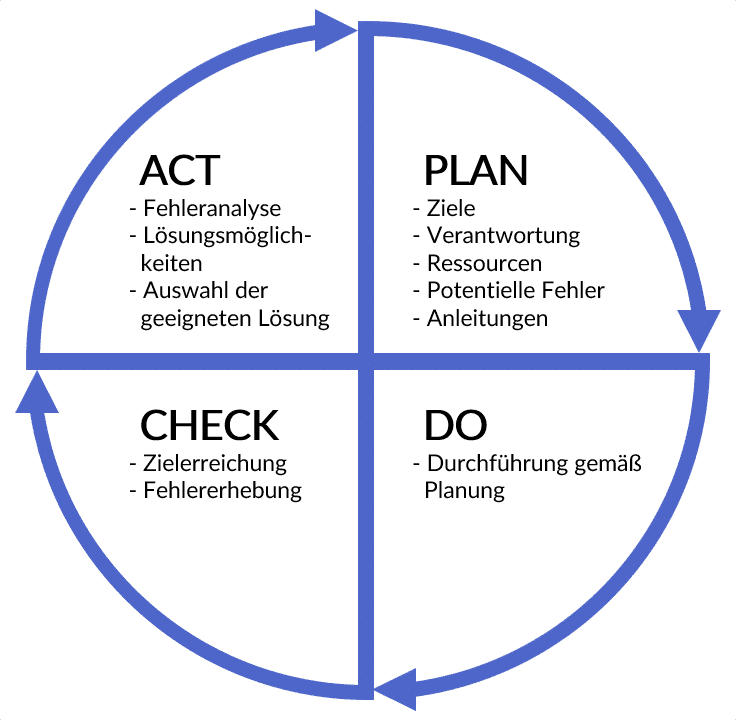