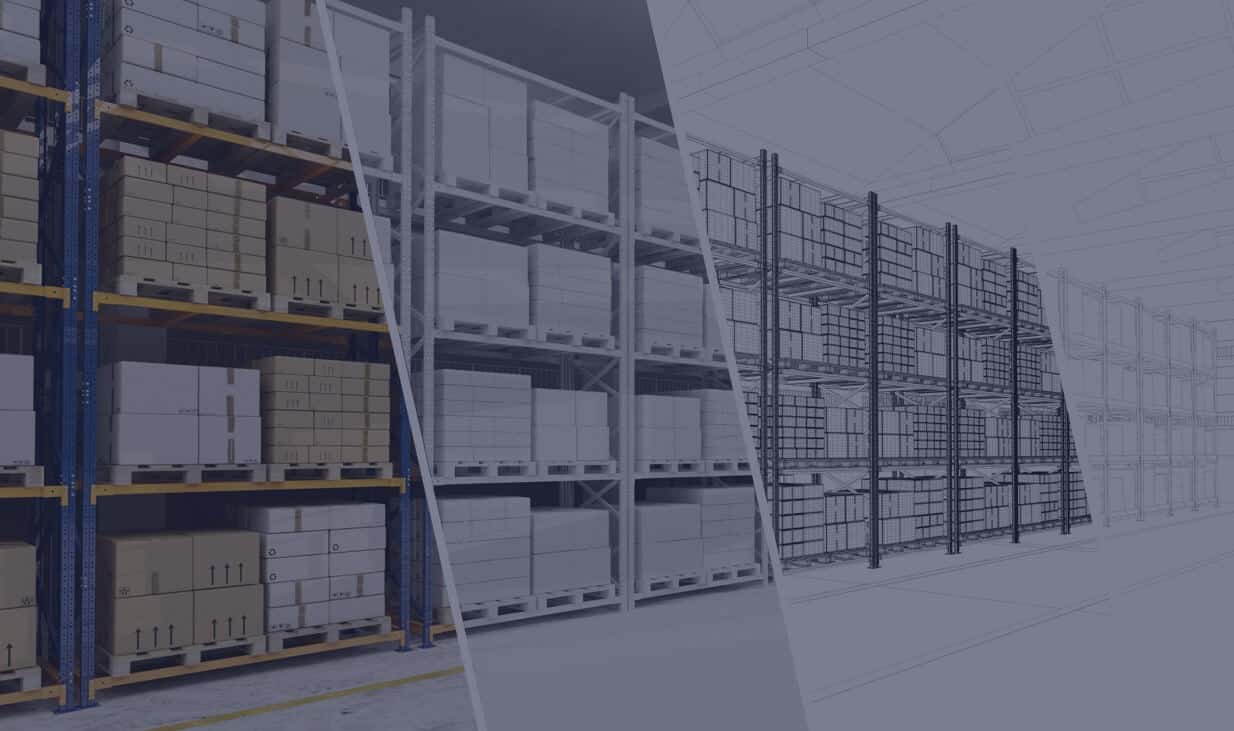
Warehouse planning – advice from our warehouse planners
Our warehouse planners support you with advice on warehouse planning
We are your innovative warehouse planners
Changing customer requirements induce an adaptation of warehouse structures. An ever-shorter time-to-market, batch size 1, fluctuations in demand and technological pressure are just some of the keywords that pose challenges for the industry. In order to provide suitable answers to these complex issues, we have developed an innovative approach to warehouse planning in order to achieve optimal goals. In this way, we ensure the innovative capacity of companies and increase both their economic and production effectiveness.
The four components of warehouse planning
In warehouse planning, our warehouse planners structure the consultation into four components: organization, technology, unit and layout. All four elements are interdependent and must be processed iteratively and in parallel. Accordingly, the warehouse process can be optimized using the warehouse organization solution module, whereby flexible storage areas are defined as well as specific delivery concepts. In the technology component, suitable storage and transport technologies are selected and included more closely in the planning before the storage unit, including the storage aids, is defined and the final layout is designed.
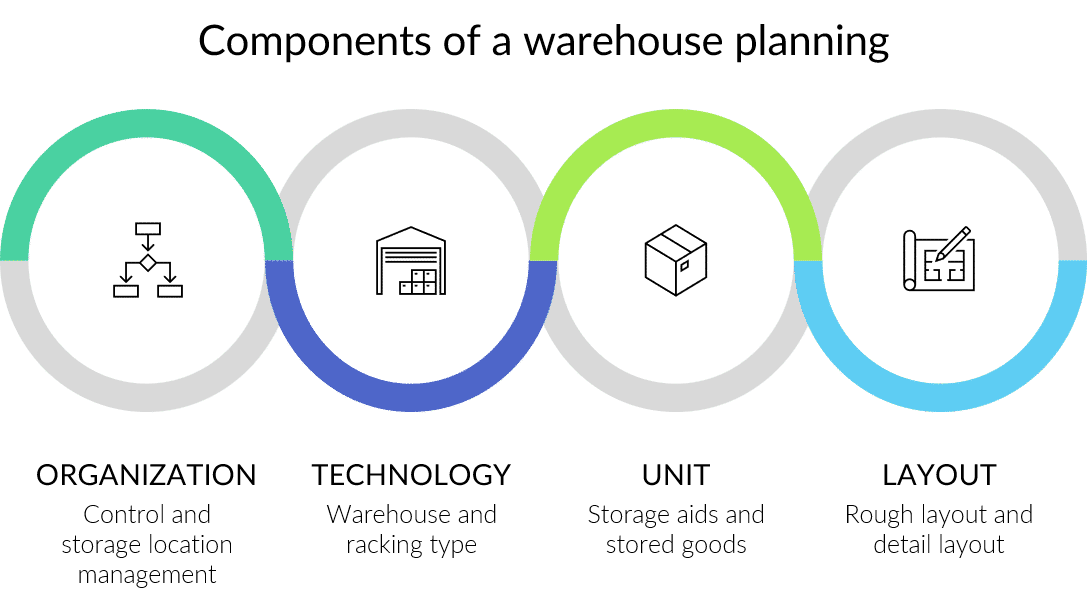
Do you need support and advice on warehouse planning?
We at Bross have been providing our clients with our expertise in planning and consulting for warehouses, especially high-bay warehouses in accordance with VDI 3656, for many years. So that you too are on the right path to professional warehouse planning.
Warehouse planning procedure
Read more about our innovative warehouse planning approach below.
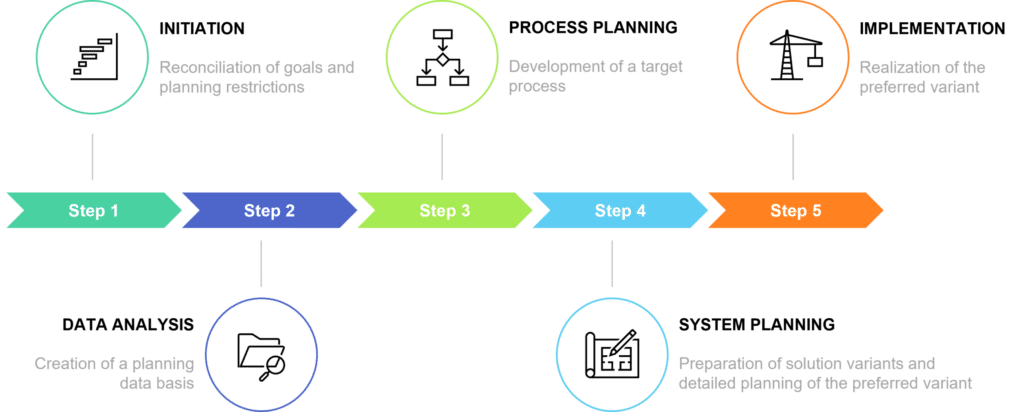
1. Initiation of the planning of a warehouse
The first step in our warehouse planning procedure is initiation. During initiation, the objectives to be achieved must be formulated and planning restrictions identified. Based on this information, we can analyze and evaluate our customers’ warehouse structures. In doing so, we rely on close cooperation with our customers in order to be able to respond to individual wishes and suggestions.
2. Data analysis as the basis for warehouse planning
The data analysis provides us with all the parameters relevant to the dimensioning of our target system. These include the master data of the products to be stored as well as the movement data and performance data of the warehouse. In addition to the product types, the dimensions and weight are also important master data. Properties such as explosive or flammable are also important information for warehouse planning. In addition, it is important to know which load carrier is to be stored, such as a pallet or a small load carrier (SLC). Performance data includes information such as the number of stock movements such as storage and retrieval. We use pioneering data mining methods (CRISP-DM) to carry out a comprehensive yet structured data analysis. This makes it possible to record and cleanse data from all areas (incoming goods, outgoing goods, production supply) and ultimately obtain information.
3. Process optimization in warehouse planning for lean processes
Step 3 in our warehouse planners’ approach is process planning. Based on the actual process and the knowledge gained, we derive process alternatives. Not only are the restrictions, goals and wishes of our customers always taken into account, but the number and height of storage levels are also examined in order to avoid unnecessary storage at the wrong point in the value chain. To realize the customer’s requirements, we work closely together to develop the optimal process iteratively.
4. System planning of solution variants in warehouse design
For the technical implementation of the planning project, requirements are drawn up that represent the framework conditions of the target system. These requirements are compared with a specially developed catalog and suitable systems are selected. The catalog lists all manufacturers such as SSI Schäfer, Swisslog, Jungheinrich, Knapp and others, and their solutions such as miniload systems, warehouse lifts, AutoStore, automated guided vehicles (AGV), etc. are listed and characterized. We present these systems to our customers as roughly planned variants. Based on our recommendations and the customer’s ideas, the preferred variant is selected and planned in detail according to the warehouse circumstances. Possible solutions range from manual to fully automated warehouses.
5. The realization of warehouse planning
The final step in the warehouse planning process and consultation is support during implementation. During the realization of the concept, we are always at your side as a strong implementation partner. We provide support with the preparation of all tender-relevant documents. Based on years of industry experience and project-specific characteristics, we recommend (sub)trades and establish initial contact. By obtaining offers from various providers, we narrow down the selection of offers according to your objectives and present them to you in detail. In addition, once the warehouse planning project has been awarded to a suitable industrial partner, we take over all coordinative and organizational activities from the ground-breaking ceremony to the acceptance of the facility.