Automated guided vehicles AGVs – procedure and advantages
Automated guided vehicles – AGVs for short – have long been established in modern factories. Once installed, they take over automated tasks during operation and ensure an efficient material flow. Driverless transport vehicles – AGVs for short – are one component of the automated guided vehicle system. These transport pallets, pallet cages or small load carriers. On the other hand, an AGV consists of load transfer and load pick-up stations. The AGVs are navigated using inductive or optical line guidance or freely using laser scanners with or without reflectors. AGVs operate in so-called taxi mode (source and sink flexibly depending on the order), flow line mode (same sequence of sources and sinks, mainly for assembly activities) and in mixed forms. An AGV can be taken out of the system and loaded, e.g. when it needs to be loaded. The AGV receives its orders via a central control system or directly at the vehicle. The vehicle is in constant communication with its environment via its master control system and ensures that the doors are opened, for example.
What are the advantages of an automated guided vehicle?
Driverless transport systems have many advantages compared to conventional manual industrial trucks such as forklifts or permanently installed conveyor technology:
- Support with repetitive activities such as driving from A to B
- High availability around the clock
- More transparency thanks to defined travel routes and times
- Reduced risk of accidents thanks to high safety standards
- Reduction of personnel costs
- Full flexibility thanks to routes that can be changed at any time
- Consistent and low throughput times
- Minimisation of transport damage and incorrect deliveries
What is the procedure for planning an automated guided vehicle system?
The planning of an AGV begins with conceptualisation. This involves collecting the requirements for the transport task to be conceptualised. The requirements for describing the transport task are defined in the VDI 2710 guideline. The requirements can be found in the following diagram:
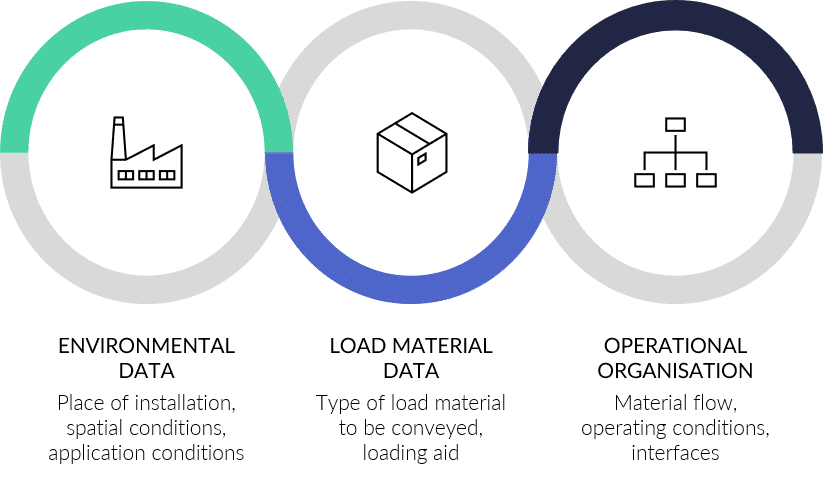
What AGV solutions are available on the market?
After conceptualisation by listing the requirements for the AGV, these are compared by Bross with a market overview. An extract of AGVs from established manufacturers such as Linde, Jungheinrich, KUKA, Gebhardt, DS Automotion, EK Automation or Still can be found in the following overview.
What costs and investments need to be considered in the business case?
In a business case, the level of investment is compared with the annual savings potential. We therefore first look at the investment side. In addition to the acquisition costs of the AGV itself, the installation of an AGV requires an enormous amount of planning. The planning of the route network is particularly complex. This planning effort must be factored into the investment calculation. In addition to the costs for the AGV, the costs for the other system components, consisting of the load transfer stations and the AGV control system, must also be taken into account. Operating costs for energy and maintenance are incurred as running costs. The savings potential of a monetary nature weighs most heavily on personnel costs. An AGV also offers many other potential savings in terms of time, such as a reduction in throughput time. Furthermore, there is no need for personnel planning, for example for forklift drivers.
Load-pulling AGVs (e.g. tractors)
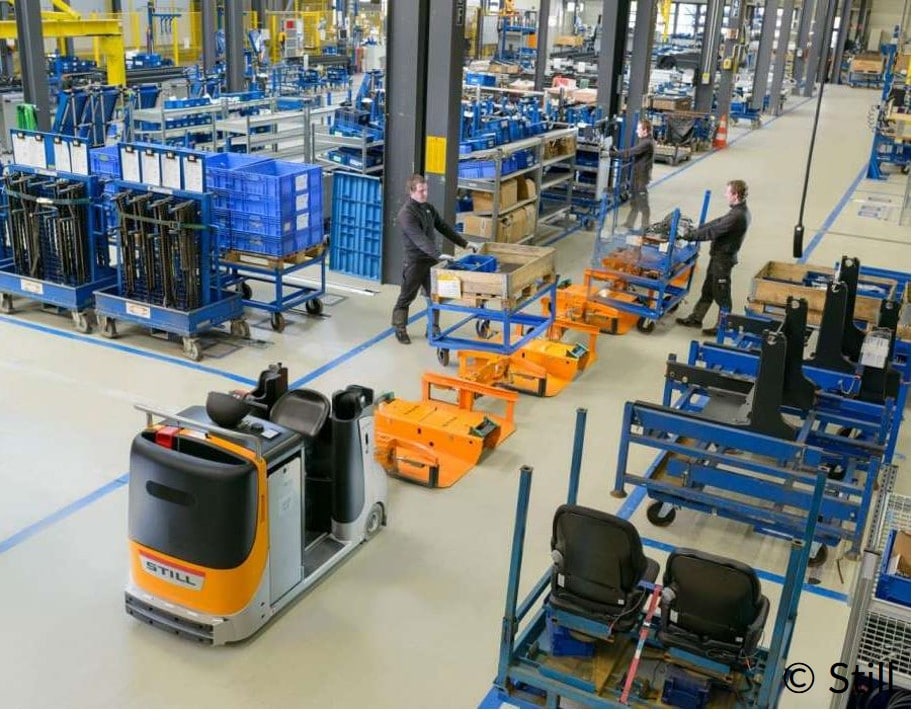
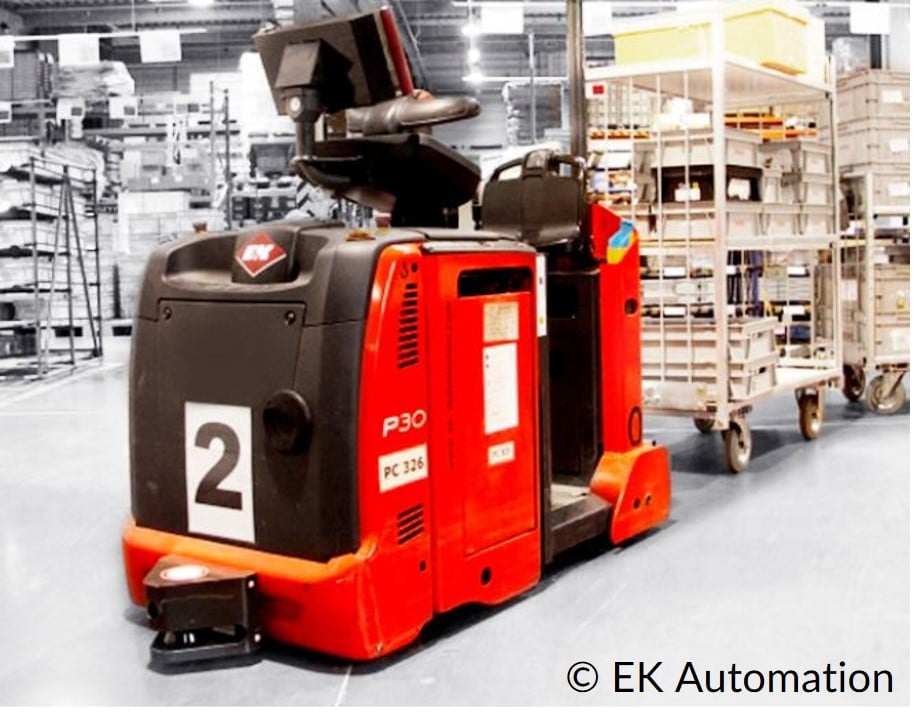
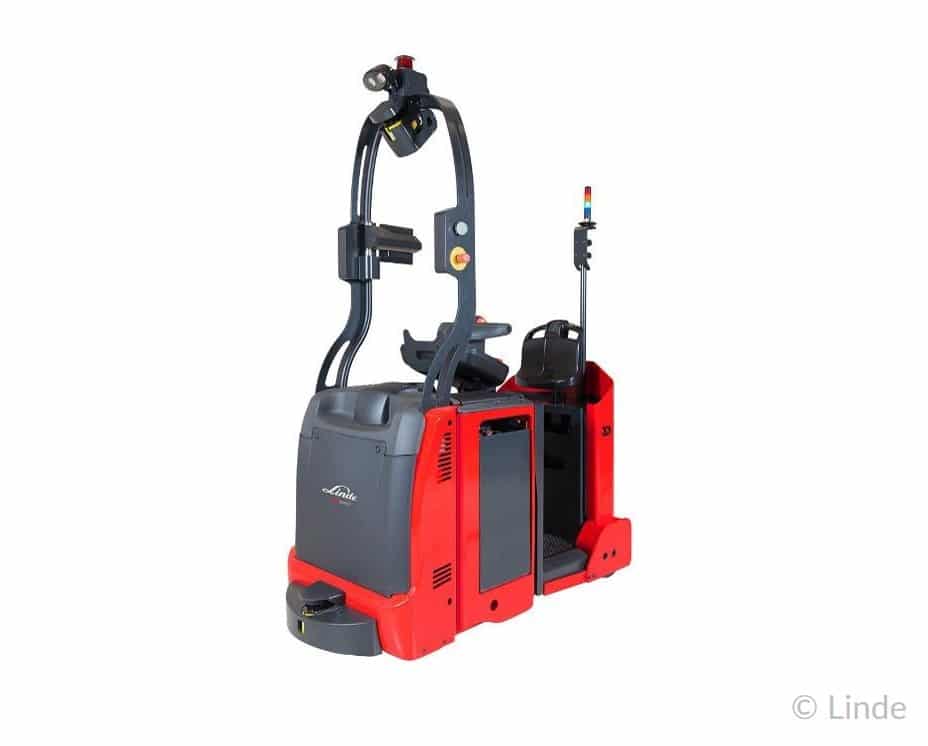
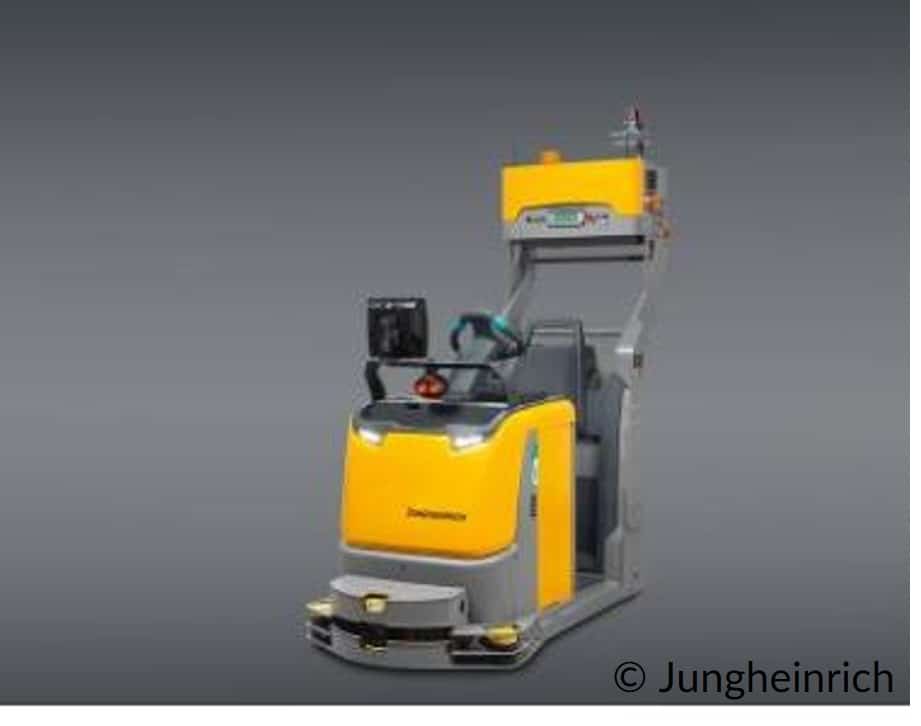
Load-bearing AGVs (e.g. with forks)
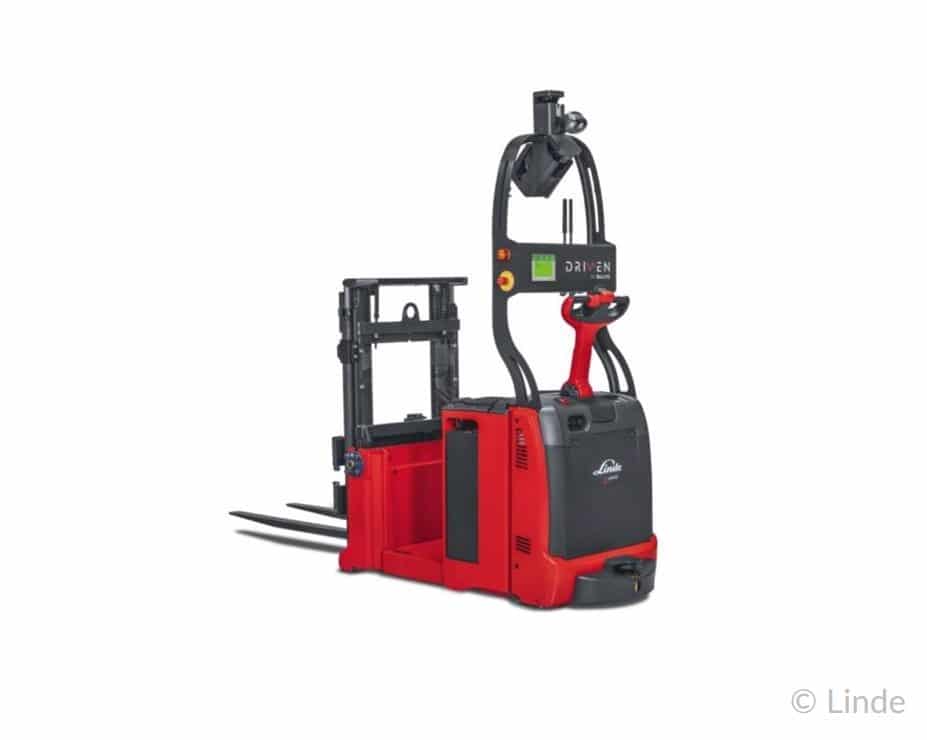
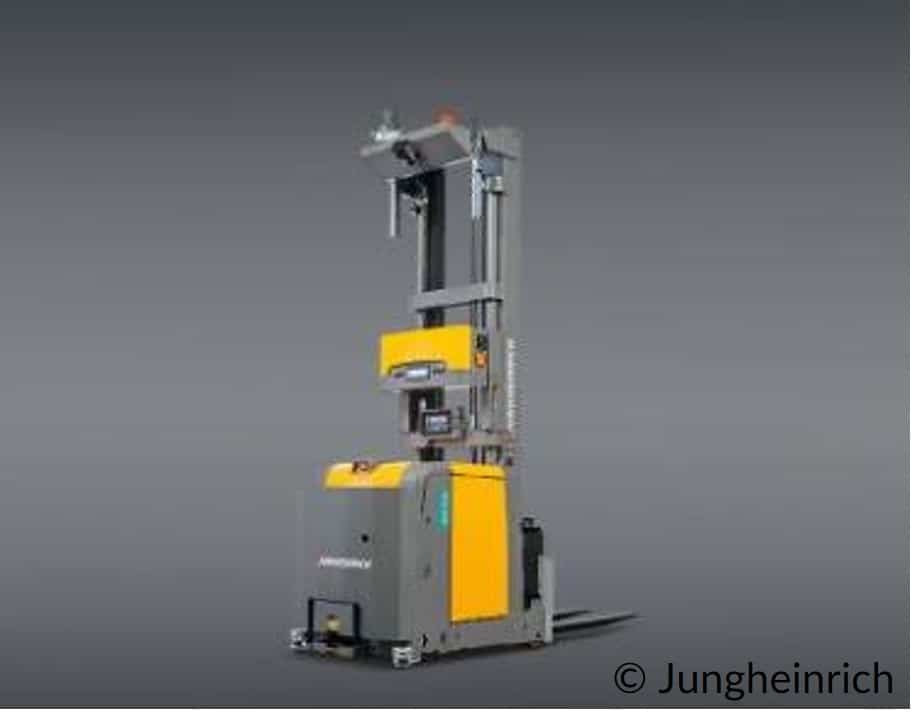
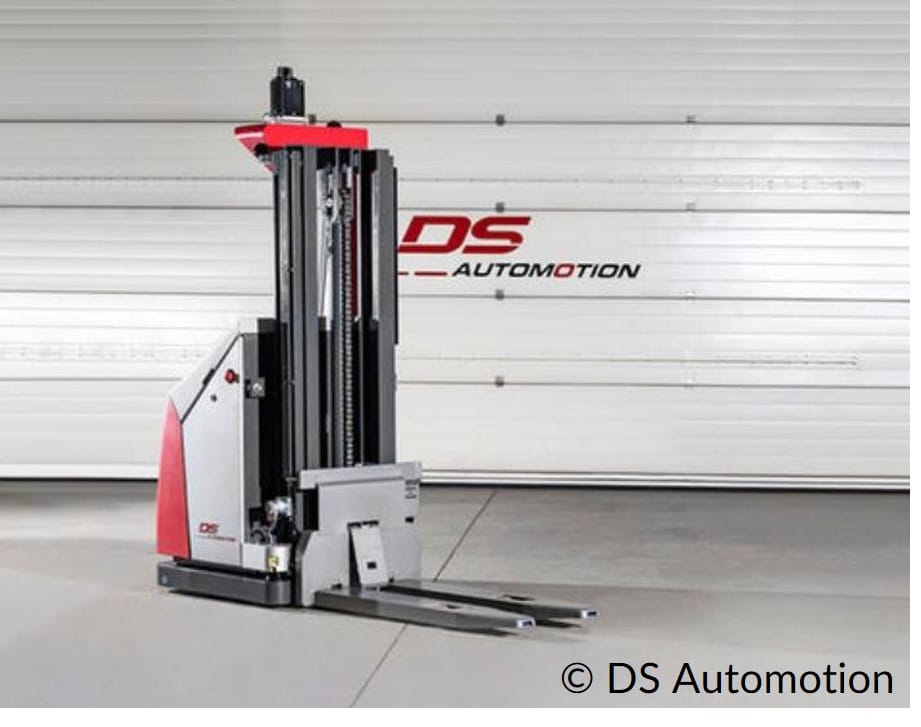
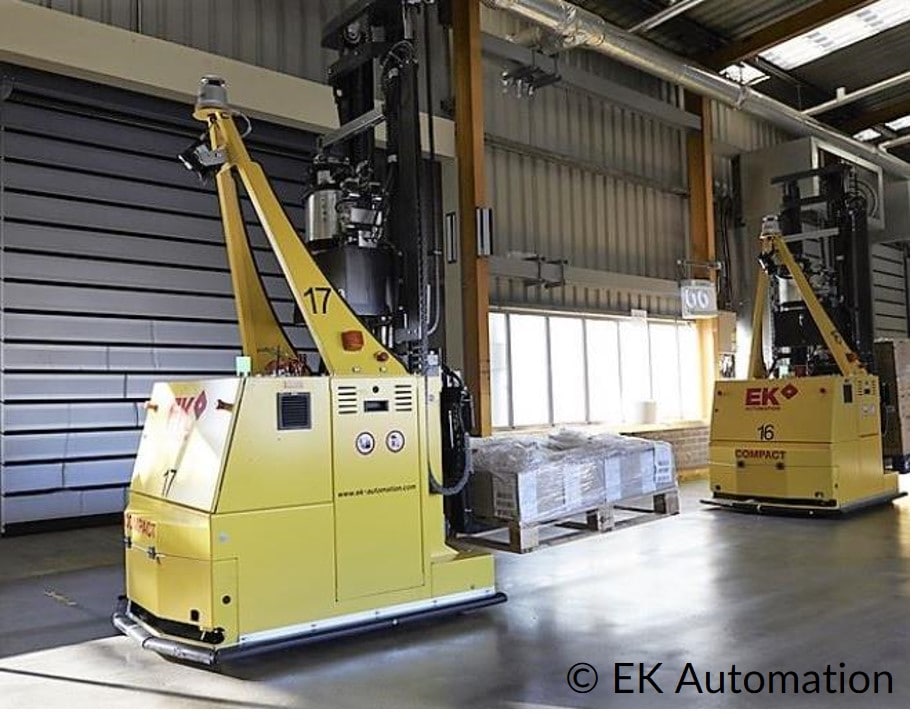
Load-bearing AGVs (e.g. with lift table)
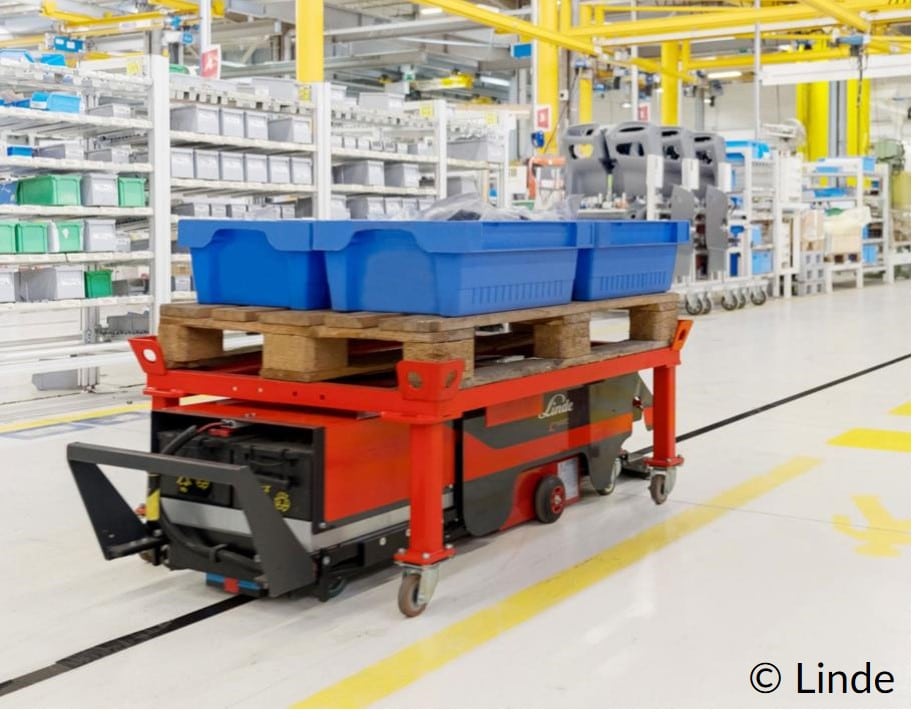
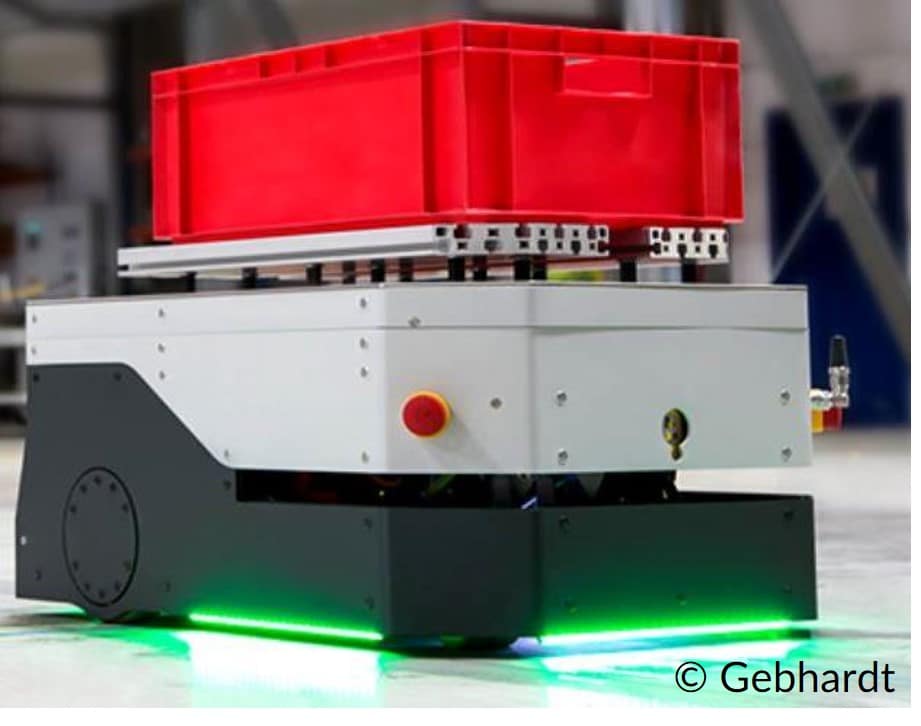
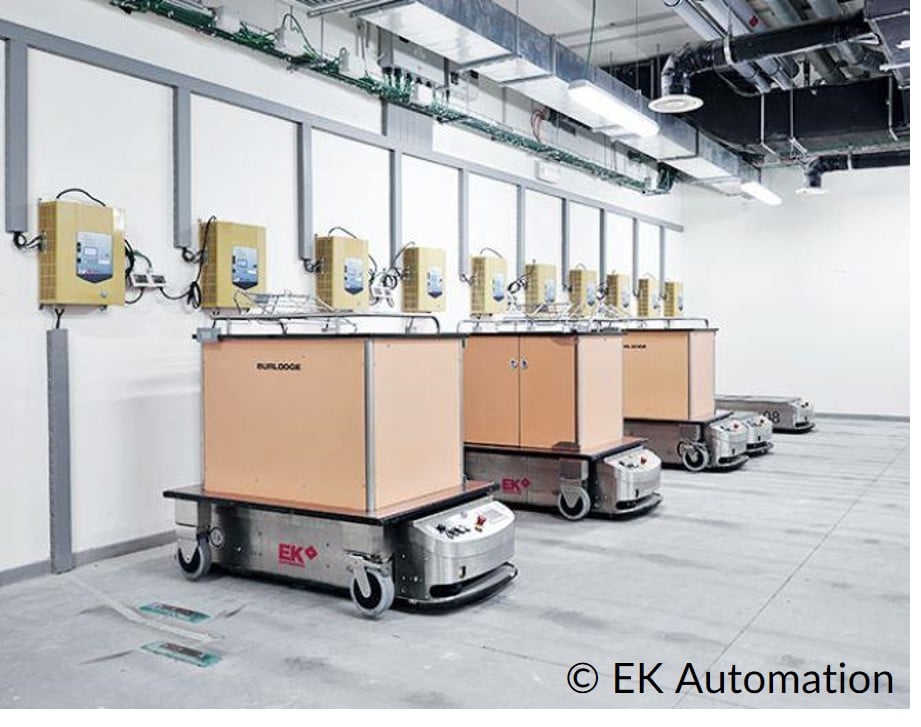
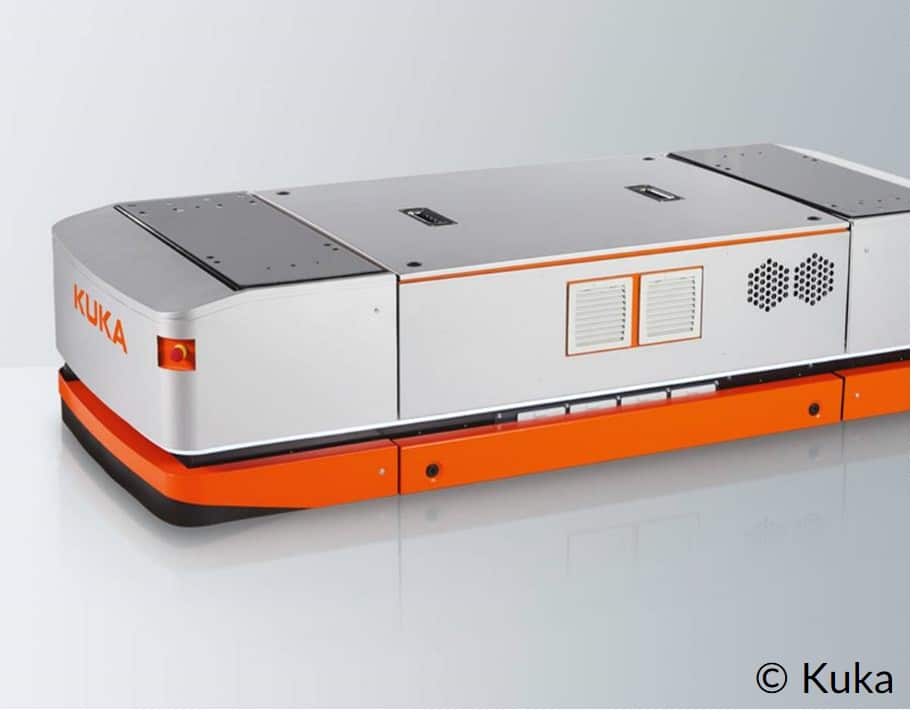
How safe are automated guided vehicles?
AGVs are equipped with comprehensive sensor technology. All-round sensors enable safety in every direction in all operating modes. Personnel protection scanners in the drive direction, side scanners and personnel protection scanners in the load direction ensure contactless safety around the vehicle. The scanners create two virtual fields around the AGV, the warning field and the protective field. If a person is detected in the warning field, the AGV quickly reduces its speed in milliseconds. If a person enters the narrower protective field, the AGV stops immediately. The protective fields are dynamic; they adapt to the current speed of the AGV. The higher the speed, the wider the warning and protective field. The AGVs even react to unexpected signals as they scan the route. The AGV is also prudent in its own behaviour. It emits visual and acoustic signals, for example during the loading process. The automatic tug gives an acoustic signal before continuing its journey and then travels at a reduced speed for the first few seconds. This gives the operator sufficient time to move away from the trailers. The AGV always uses the same routes and does not deviate from them. If the route is used by the automated guided vehicle and personnel at the same time, increased path widths must be used. Floor markings and appropriate warning signs are of course a must.
What rules of conduct apply when working with AGV?
Despite the many safety features built into an AGV, it is important to minimise the risks through your own behaviour. The AGV comes with a few rules to ensure smooth cooperation:
- Driveways must be kept clear
- Never step into the track directly in front of the AGV
- The AGV always has right of way to work efficiently
- Always stay out of the danger zone when charging.
- Elevated objects cannot be detected by the sensors and must not protrude into the path of travel